Table of contents
In a world where technology and fashion often intersect, one groundbreaking innovation is reshaping the industry – 3D printing. Imagine owning a unique piece of clothing or accessory, tailored to your precise measurements and completely customisable in terms of design. Too good to be true? Not anymore. The advent of 3D printing in the fashion industry has made this vision attainable. This article explores the fascinating realm of 3D printed fashion – its inception, how it works, its benefits and future perspectives.
Origins of 3D Printing in Fashion
The advent of 3D printing, or additive manufacturing, as it is often referred to, has revolutionized various industries, with its intersection with fashion marking a new era of design possibilities. The evolution of 3D printing in the fashion sector began with adventurous designers willing to venture into unexplored territories. These pioneers recognized the potential of this innovative technology in shaping the future of fashion, bringing conceptual ideas into reality.
During the early adoption phase, forward-thinking designers pushed the boundaries of traditional fashion by producing tangible accessories and garments using 3D printing. This not only opened up new avenues for creative expression but also redefined the way clothes and accessories were designed, manufactured, and used. The incorporation of this groundbreaking technology in fashion has unlocked endless possibilities, reshaping the concept of wearables and fashion design in general.
The fusion of technology and fashion has undoubtedly spurred a significant transformation in the industry. The utilization of 3D printing has moved beyond just a novel concept; it has established itself as a dynamic and powerful tool that continually redefines the landscape of fashion design.
The Mechanics Behind The Magic
The enchantment of 3D printing in fashion is not just a result of majestic designs and innovative aesthetics. The real magic lies deep within - in the mechanics and the methodology used to transform abstract concepts into tangible realities. The key is in the layering techniques employed.
One of the commonly used techniques is Fused Deposition Modeling (FDM). FDM is a technique that utilizes heat to melt a specific material, often a plastic filament, and then extrudes it layer by layer. This systematic process continues until the designed object gradually takes shape. This technique is particularly favored due to its accuracy and the level of detail it allows, making it perfect for creating intricate designs.
However, the technique is only part of the equation. The material used plays a significant role in the final result. The materials must be malleable to a certain degree, allowing them to be easily manipulated without breaking or losing their form. This malleability is what makes some materials more suitable than others for 3D printing in fashion. Various materials including plastics, resins, and even metals can be used, depending on the design and the desired end product.
In summary, the magic behind 3D printing in fashion lies in the perfect harmony between the right technique, in this case, FDM, and the use of suitable, malleable materials. This combination brings to life the intricate designs that have been revolutionizing the fashion industry.
Beyond Aesthetics - Functional Benefits
The blend of high-tech innovation and fashion goes beyond just aesthetics. One of the significant perks of this merge is the creation of bespoke fits. With the advent of 3D printing in the fashion industry, garments can now be crafted with precise customization, thereby providing superior comfort to the wearer. This technology allows every intricate detail to be captured, resulting in a fit that is unique to the individual.
Moreover, the use of bio-plastics in the production process offers an environmentally friendly alternative. Bio-plastics, often used in additive manufacturing, have the potential to change the face of fashion by providing sustainable solutions. The use of such materials results in the reduction of waste and carbon footprint, thus leading the way to environmental advantages. The fashion industry, notorious for its environmental impact, can greatly benefit from this high-tech blend, making 3D printing not just a style statement, but also an eco-friendly alternative.
Redefining Accessibility & Affordability
In the realm of high-fashion, the concept of 'democratization' is garnering significant attention. With the advent of affordable home-based kits, this revolution has been gaining momentum, challenging the long-standing exclusivity that is often associated with couture pieces. These kits are harnessing the power of consumer-grade printers, making the world of fashion more accessible and less daunting for those outside of the traditional fashion circles.
Previously, couture fashion was seen as a luxury reserved for the elite. It was not just the steep price tags, but also the rarity and the craftsmanship that came with these pieces that made them out of reach for the average consumer. However, the landscape of fashion has been changing, and much of this change can be attributed to the technological advances in 3D printing.
With the rise of consumer-grade printers, an unexpected door has been opened in the world of fashion. These printers, often part of affordable home-based kits, are capable of creating intricate and unique designs, making couture pieces—once considered unattainable—available to anyone with the interest and a basic skillset. The advent of this technology is not just breaking down barriers, but it is also shaping a new, more inclusive fashion culture, thus redefining accessibility in the fashion industry.
Similar
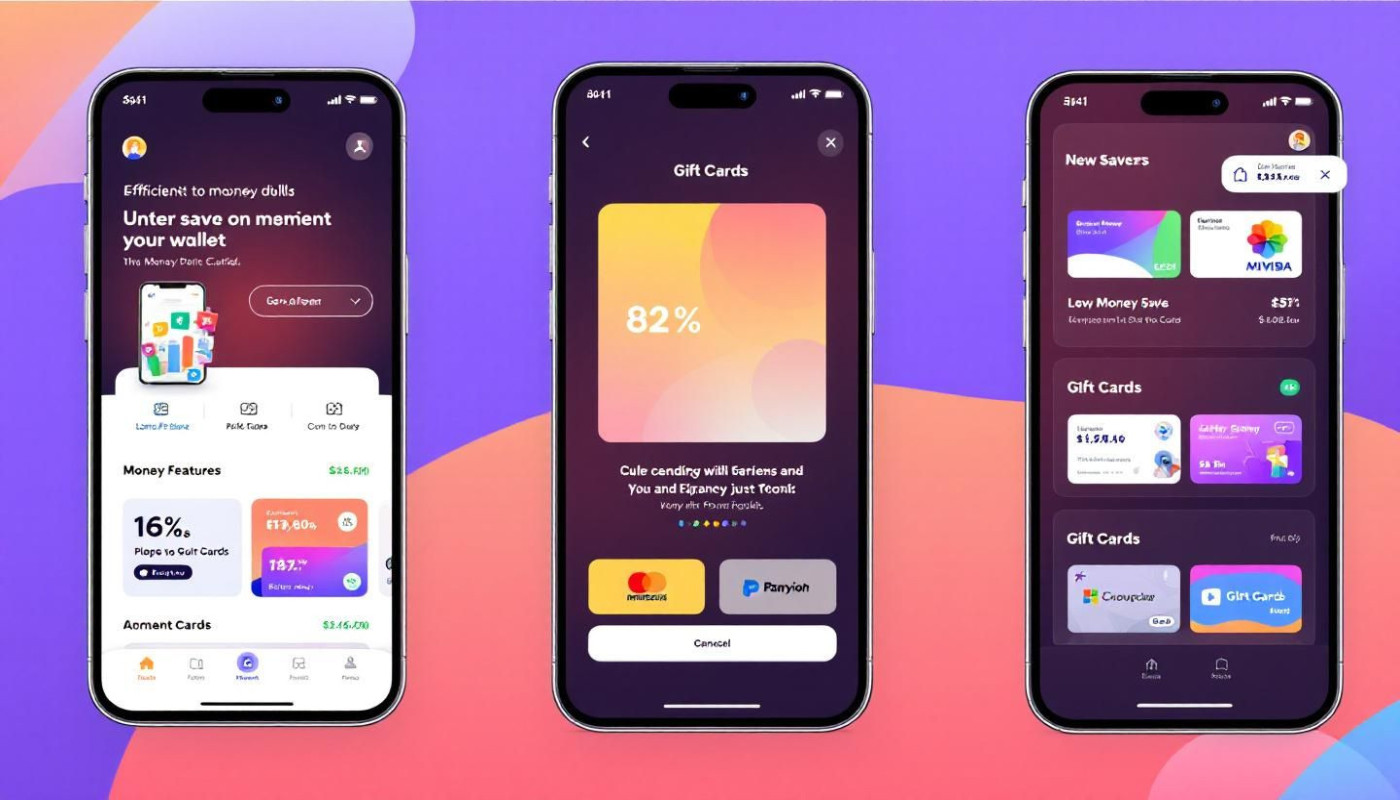
How To Save Money On Digital Gifts And Games Purchases
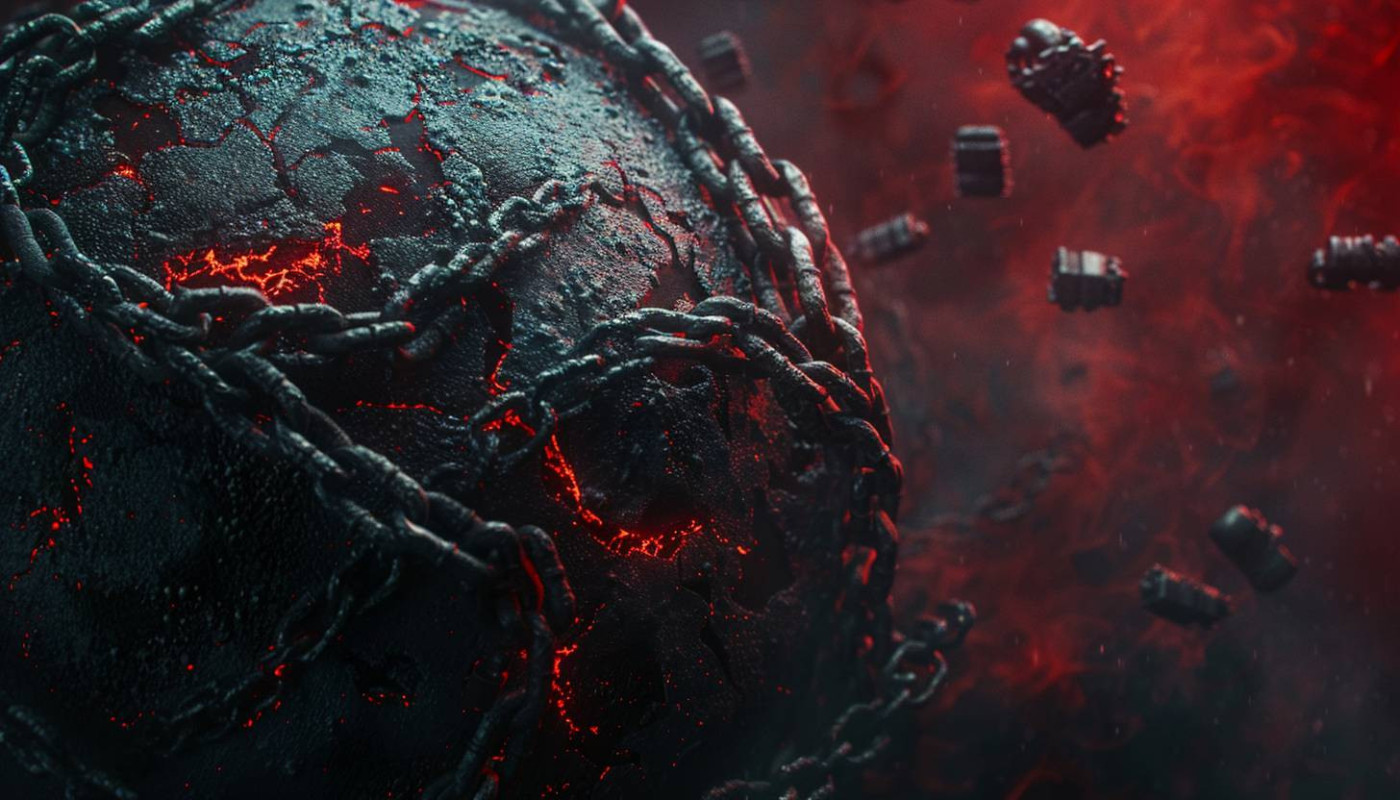
Exploring The Impact Of Ransomware On Global Economic Stability
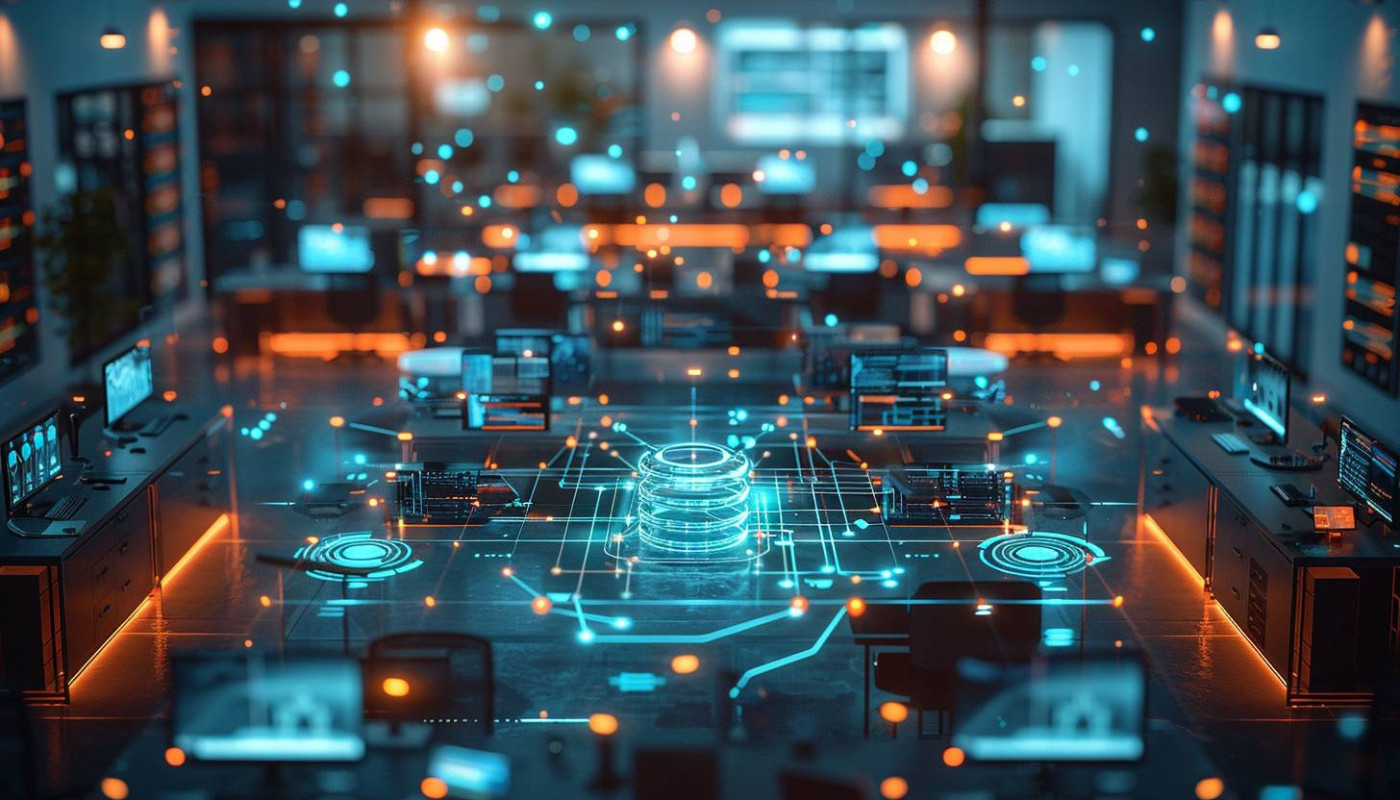